Description
Model equations and turbulence models
The Navier-Stokes equations usually form the basis of CFD. Simpler models such as Euler and potential equations are also used for special applications. In industrial applications, turbulence is often taken into account using Reynolds-Averaged Navier-Stokes (RANS) and additional turbulence models. Turbulence-resolving methods such as Direct Numerical Simulation (DNS) and Large Eddy Simulation (LES) enable detailed analyses of small-scale flow-physical effects, but require longer computing times. At the Institute, LES and DNS are used in particular in fundamental investigations and in the analysis of turbomachinery.
Computational fluid dynamics in research
CFD is an essential part of research at the Institute of Turbomachinery and Fluid Dynamics. It is not only used for the efficient design and analysis of turbomachinery, but also in fundamental fluid mechanics investigations using methods such as Direct Numerical Simulation (DNS) and Large Eddy Simulation (LES). These provide detailed insights into small-scale flow physics effects.
Areas of application and software packages
Our CFD simulations are used in a wide range of areas such as turbomachinery, wind turbines, biomedical engineering and general process engineering flows. We use specialized software for precise results, including:
-
Adapco StarCCM+
StarCCM+ is a commercial flow solver based on the finite volume method. At the Institute of Turbomachinery and Fluid Dynamics, this software is mainly used to calculate two-phase flows and the flow of porous media in the research field of biomedical engineering. The volume-of-fluid method (VoF) is used for modeling two-phase flows. STAR-CCM+ offers possibilities for individual expansion through the implementation of user-defined functions. For example, physical properties, grid movements and time step size can be calculated in user-defined functions at runtime and returned to the program. These functions are integrated into the CFD model via the GUI.
-
ANSYS CFX
CFX is a commercial solver for unsteady three-dimensional single and multiphase flows. It is used in the TFD for the simulation of exhaust turbochargers, axial machines, wind turbines and general fluid mechanics problems.
-
FLOWer
FLOWer is a structured RANS solver developed by the German Aerospace Center (DLR) specifically for external flows. In FLOWer, steady and unsteady simulations can be carried out using various turbulence models. The Chimera technology in FLOWer makes it possible to move several meshes relative to each other and to determine the flow variables for the entire field.
-
LESSOCC2
LESOCC2 (Large-Eddy Simulation On Curvlinear Coordinates) is a flow solver developed by the Karlsruhe Institute of Technology (KIT). It solves the three-dimensional, unsteady, filtered and incompressible Navier-Stokes equation. Small-scale turbulence is modeled by the Smagorinsky model.
-
MISES
MISES is an analysis and design tool for turbomachinery cascades developed by the Massachusetts Institute of Technology. It is based on a zonal coupling of viscous boundary layer and wake flow and frictionless external flow. It is used at the TFD for preliminary design and has also been expanded to include modeling of the influence of riblets on the boundary layer.
-
Numeca FINE Turbo
The commercial CFD package FINE/Turbo from Numeca is used at the TFD in particular for CFD simulations of axial and radial turbomachinery. The IGG/Autogrid mesher included in FINE/Turbo also allows fast, template-supported meshing of three-dimensional and complex geometries such as non-rotationally symmetrical hub contours, cooling geometries in turbine blades and cavities.
-
OpenFOAM
OpenFOAM is an open source simulation package for any continuum mechanics problem. It is based on an unstructured finite volume method, contains a large number of solvers and also allows object-oriented programming of your own solvers. OpenFOAM is used in the TFD for large-eddy simulation.
-
TRACE
TRACE (Turbomachinery Research Aerodynamic Computational Environment) is a program system developed by the DLR Institute of Propulsion Technology and MTU Aero Engines for the simulation of three-dimensional unsteady flows in turbomachinery. The TFD uses TRACE in a large number of research projects to simulate all types of thermal turbomachinery. The spectrum of applications ranges from compact compressors and test rigs to entire engine turbines. In addition, physical models for turbulence and transition are developed at TFD.
-
XFoil
XFOIL is used at the TFD to calculate the aerodynamic profile coefficients (lift and drag) of wind turbines. XFOIL is based on a panel method and was developed at the Massachusetts Institute of Technology (MIT) for the design and analysis of subsonic airfoils.
Contact person
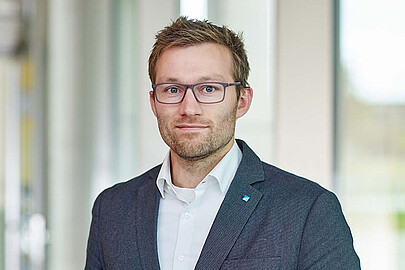
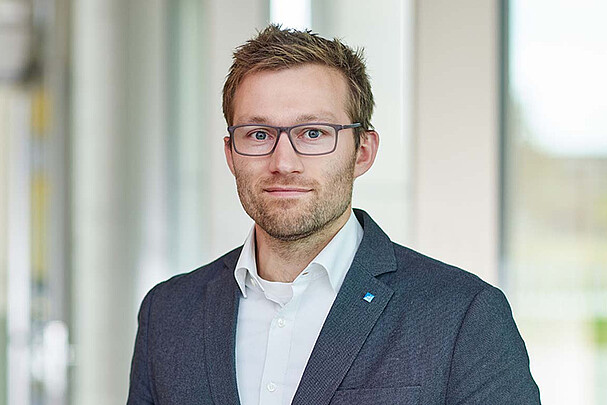
30823 Garbsen
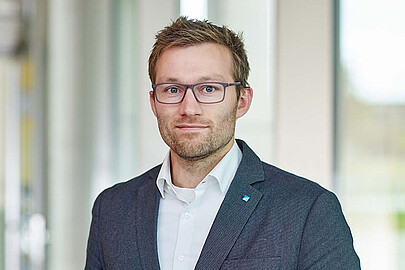
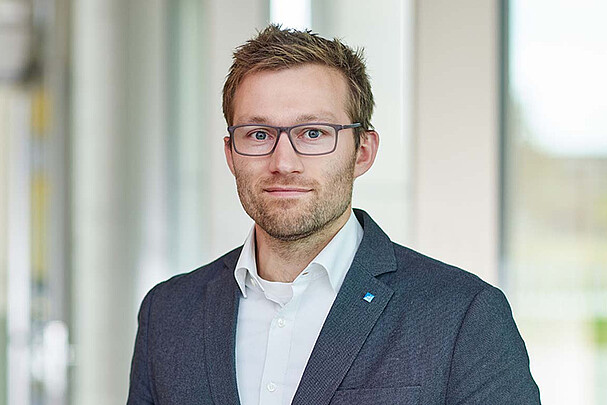